2017年3月7日,针对风电机组轴承突出的故障“轴承跑圈”问题,中国风能协会名誉主任贺德馨先生邀请了几位目前已经退休,与企业没有直接利益关系的风电行业的老技术专家,在中国船级社认证公司召开风电轴承“跑圈”故障研讨会。出席此次研讨会的资深专家还有:风能协会资深委员姚小芹、华能新能源公司原副总工程师王斯永、杭州前进齿轮箱集团股份有限公司原总工程师宣安光、南京高速齿轮箱集团公司原副总工程师郭宝霖、中国轴承工业协会顾问、原西北轴承公司总工程师何加群、河南科技大学教授叶军等。在结合专家现场讨论及后期资料整理的基础上形成了该报告,现对外发布。
与会专家一致通过成立“风电技术˙专家研讨”平台,该平台是一个非盈利的风电技术研讨公共平台,常设在中国船级社认证公司,会议推选王斯永为“风电技术˙专家研讨”主任委员,姚小芹为副主任委员,秘书处设在中国船级社认证公司,联络人为陈鸿雁。今后将定期召开技术研讨会,聚焦风电行业高发故障,并形成成果报告,供风电行业内各有关方面和政府决策机关参考。
一、轴承“跑圈”问题的现状
所谓轴承“跑圈”,就是轴承的外圈与轴承座或者内圈与轴产生了相对运动。变速箱的行星齿轮发生跑圈,会对变速箱产生不可修复的损毁。
从2015年年初开始,运行的风电机组逐渐暴露出变速箱轴承“跑圈”的问题。根据不完全统计,近年来我国装机运转的十万多台机组中,发生“轴承跑圈”故障占10%以上,不仅是轴承应用较多的双馈电机型机组,就是主传动系统轴承较少的直驱机组也发生了类似的故障,其总数也超过了1000台。根据一个电力设备研究机构的人员最近抽测一批在运机组的结果,振动频谱显示相当高比例的机组存在跑圈的问题(按照他们的说法是几乎百分之百)。国外厂商的部分机组也存在轴承跑圈问题。从发现的轴承“跑圈”的总体情况看,变速箱高速端比例较高,行星齿轮轴承“跑圈”的比例较低。但是在个别几个厂家的产品中,行星齿轮轴承“跑圈”的比例比较高,出现批量故障。
轴承跑圈造成的损失会大大提高风电机组的运维成本,对未来保险公司保费费率也可能产生影响。
目前,国内多数发生轴承跑圈的整机厂家、开发商、保险公司并不了解这个情况,故障都是由变速箱厂自己处理,并未如实告诉客户变速箱损毁的原因。这种情况,导致这种高风险、高成本的故障成为风电运行和保险行业巨大的潜在风险。
对于变速箱高速端轴承“跑圈”故障的处理多数是在故障发现后,采用镶套或使用聚合物粘结剂的方法解决。这两种方法在地面设备上有比较成熟的经验,但是对于风电机组变速箱高速端轴承,是否可以保证修复后长期使用,目前尚无成熟经验。
对于行星齿轮轴承“跑圈”,目前国内还没有提前发现“跑圈”故障的成熟技术,而且由于机组形式和运行环境的差异导致轴承“跑圈”的频谱的差异,因此绝大多数行星齿轮轴承“跑圈”故障是在变速箱损毁后确认的。
对于直驱机组主轴承跑圈,在轴承未发现明显损伤的情况下,采取再调整轴承游隙的办法处理;若轴承损伤,则更换主轴承。
二、轴承“跑圈”问题的分析
究其根本是由于轴承选型不当、结构设计和载荷设计不当、制造过程中工艺控制不当、轴承游隙调整不当、轴承润滑不当、设备储存或运输不当等原因,使得轴承滚子和轴承滚道发生比较严重的滑动半干摩擦,最终导致轴承“跑圈”。
1. 主轴轴承
(1)采用双列调心滚子轴承的兆瓦级风电机组的主轴轴承,同时承受轴向及径向的载荷,失效的概率较高。这是由于双列调心滚子轴承的游隙较大,上风向侧的轴承承受载荷很小,大部分径向载荷和轴向力由下风向轴承承受,造成滚子过多的打滑,加上润滑不良使材料发生从点蚀到粘附剥落,座圈和滚子以及保持架受力不均发生变形,改变了座圈与轴承座的配合,出现“跑圈”、卡死等常见故障。
(2)新的传动系统设计时,主轴轴承已很少选用调心轴承,推荐选用圆锥滚子轴承,径向和轴向承载能力强,可通过预紧使滚子均匀受载,滚子不易产生滑动摩擦。但是,由于安装工艺对装配工人的经验和技术要求比较高,轴承游隙调整不当依然可以引发半干滚动摩擦,继而出现跑圈故障。
(3)轴承装配采用热装法。由于没有足够尺寸加热装置,而采用局部加热法,加热不均匀,造成轴承变形。
(4)运输过程中机组减震措施不当,或轴承某一部分长时间承重,造成滚道局部变形。
(5)目前在运的风电机组主轴轴承的润滑方式主要有两种:润滑脂润滑及压力润滑油润滑,其中使用润滑脂润滑比例较高。风轮的转速一般在10-20转/分,低转速导致主轴轴承和行星架支撑轴承的油膜形成往往比较难。若油膜厚度不足以隔开两个金属表面,则润滑没有达到预定的效果,轴承就会发生早期磨损,产生材料剥落的损伤,发生半干滑动摩擦,继而导致轴承跑圈。压力润滑方式对改善轴承的工作条件十分有利,除了及时形成油膜保护滚道滚子之外,还能带走热量和磨粒,延长使用寿命。推荐有条件的情况下,主轴轴承也使用压力油润滑。
2. 变速箱轴承
变速箱中高速轴侧轴承发生跑圈的比例高于行星轮轴承。两者发生的原因是不同的。
高速轴侧轴承
(1)轴承与轴承座的配合公差选择不合理,导致过盈量不足。由于风电机组运行的外部环境差别很大,选用标准公差带很可能不能适应运行条件。
(2)装配时工艺控制不严格,造成轴承与轴承座的极限上偏差与极限下偏差的配合。在装配现场实际上已经发现装配工选择过盈量小的轴承进行配装的现象。
行星轮轴承
(1)风电机组变速箱实际使用时的最大功率可能达到名义功率的3倍以上,特别是增长叶片情况下,风轮惯性矩大大增加,在机组启动和停机过程中对传动系造成的冲击载荷也极大增加。国内机组在原型机基础上增长叶片后,并未对变速箱进行相应的再设计,造成刚度相对较差的变速箱行星轴系和中间轴系出现偏载的情况,偏载则加剧轴承应力集中现象的发生,进而引发轴承跑圈。
(2)行星轮系结构设计薄弱。国家标准GB/T19073 风力发电机组齿轮箱中规定:行星齿轮轮毂厚度应不小于3倍模数,是为了保证齿轮座圈具有足够的刚度抵抗齿轮受力产生的变形。而行星齿轮的变形是轴承跑圈的重要原因之一。国内变速箱厂批量的行星齿轮轴承跑圈故障发生,恰恰是设计没有满足标准提出的齿轮轮毂厚度要求。
针对行星轴系偏载国外采用了浮动行星变速机构,以达到均载的目的。但是此类结构在变速箱装配和调整时比较复杂。
针对风电机组空间限制导致行星齿轮结构尺寸难以满足刚性要求的现状,国外提出行星齿轮与轴承外圈一体化的解决方案和铁姆肯类似的集成式柔性销方案(见图1)。国内杭齿和南高齿分别采用一体化结构和集成柔性销结构试制了几台变速箱。由于行星齿轮要根据加工工序分别在变速箱厂和轴承厂完成机械加工、热处理和产品检测,变速箱的成本大幅度提高。国内风电整机企业在目前的市场价格下,难以接受。而国外整机企业已经批量采用此类结构的变速箱。
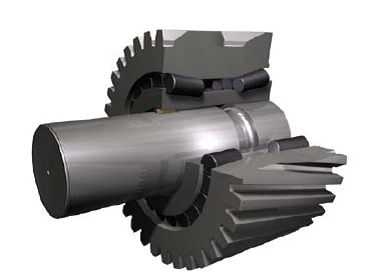
图1 铁姆肯集成式柔性销组件
三、几点建议
根据目前的现实情况提出几点建议:
1. 从目前各方面反映的情况看,对于已经投产在运的风电机组如何在破坏性事故发生前及时发现轴承跑圈的先兆是当务之急。这样可以把事故消除在萌芽之中。但是,由于风电机组的结构不同,运行环境不同,轴承位置不同,技术上尚未掌握各类轴承跑圈的振动特征谱。目前可以做的就是搜集已经发生事故的风电机组的振动监测记录,组织专业队伍进行分析,尽快从中找出规律性的东西,然后在运行风电场进行验证、推广。目前已经有若干制造企业、开发运行企业和研究机构表示愿意参与,并提供验证条件。
2. 本报告前面的分析仅仅在以往的理论、经验和可以得到的案例基础上进行的。对于当前大量发生的事故尚未全面掌握。为了进行事故分析,各变速箱制造厂不应再以保守所谓“商业秘密”为借口,而拒绝公开事故。这样做的结果只能对我国风电产业造成更深的伤害。只有行业内全面地掌握事故真实情况,针对可能的原因深入分析,才能找出缺陷根源并采取行之有效的措施加以解决。同时,为掌握事故监测预警技术提供基础数据。建议各涉及类似事故的企业应如实向整机企业、开发运行企业以及研究机构如实提供事故情况。
3. 轴承装配时应配备足够的工装器具,防止组装中的隐形损坏。过盈配合的装配最好用封闭的加热装置对轴承整体均匀加热,加热温度不宜过高,在升温过程中处于正游隙状态,不会挤压滚子而发生变形。在有条件的情况下,建议采用冷冻轴的方式装配轴承。对轴承的润滑要高度重视,除了保证充分润滑以外,还要采取足够措施确保油液的清洁度。
4. 在轴承及其配合的选用上,主机和部件以及轴承供应单位之间应密切协作,及时交流和反馈,合理选择轴承及配合。装置轴承的轴和孔应按照轴承圈直径公差选择合理的公差带,注意适当收紧公差范围以确保配合的过盈量。
5. 加强专业技术工人的培养和训练,以确保轴承的装配和游隙调整符合技术要求。
6. 装配过程中,轴系应反复对中,减轻额外载荷的影响。
7. 强化变速箱加工、装配现场的工艺规程、工艺卫生管理,确保变速箱加工、装配过程在严格的工艺条件下进行。
8. 编制风电机组与主轴的运输和保管相关的技术指南,防止在运输及非运行阶段,主轴轴承下端滚道和滚子由于承受主轴巨大重力引起变形情况的发生。
9. 增强风电机组机架的刚性,防止变形引起各轴承的非正常偏载。
10. 加强风电机组日常维护保养,严格遵守安全操作规范,对机组运转的启动、制动、停转、停用等不同过程产生的影响要有足够的应对措施。
11. 风电机组应配备相关的检测装置,对传动系统的振动、温度状态实施瞬时监控,对测量数据进行分析,准确查找原因,提前发布预警,避免因故障停机。
12. 强化风电机组设计研究,以可靠性分析为基础,针对机组所处的恶劣工况,系统分析传动系统关键部位所受的异常瞬间负荷的影响,编制更为符合实际工况的载荷谱,充分保证系统及零部件的安全裕度。改进传动系统的布局和结构,降低瞬间异常冲击载荷的影响。
13. 在积累经验的基础上合理选择机组传动系统的结构形式,尽可能采用成熟的经过论证的传动形式,对新的传动形式和结构布置,未经论证不要轻易采用。
14. 原有的轴承寿命计算理论已难以满足现代风力机齿轮箱轴承计算的要求,国际著名轴承公司提出的新的轴承寿命计算方法的相关资料制造商一般较少公开。目前,轴承寿命的计算一般根据各轴承厂商提出的寿命计算方法进行估算。轴承寿命的计算方法繁多,影响因素复杂,载荷数据匮乏、复杂载荷处理方法不完善,对机组在使用过程中经常出现的瞬间载荷、制动载荷、极限载荷等的处理完全凭经验估算。此外,在变载荷处理过程中运用的线性积累损伤理论也并不能真实反映实际破坏情况,这将导致设计计算与实际应用的差距增大。为此,建议结合风电机组的实际需要加强国内轴承寿命理论的研究。
15. 建议尽早加强满足风电高载荷容量、高可靠度、长寿命这一特殊领域的轴承设计、材料、工艺、检验技术的研究。轴承行业与风电机组制造企业、风电传动装置制造企业联合开展研究工作,为风电轴承的设计、制造积累经验,争取尽早取得突破。
原标题:“风电技术·专家研讨”第一期成果发布——关于风力发电机组轴承“跑圈”问题的分析与建议报告
