目前国内众多燃煤火力发电厂已经或正在进行多种污染物超低排放工程改造,进一步降低SO2、NOx和烟尘等污染物排放以减轻对严重雾霾天气的影响。在分析某电厂1000MW超超临界机组SCR烟气脱硝、湿法烟气脱硫以及静电除尘器运行现状的基础上,提出并实施了采用“SCR脱硝增容+低低温静电除尘器+高频电源静电除尘器改造+脱硫吸收塔提效与协同除尘”的超低排放技术改造方案。
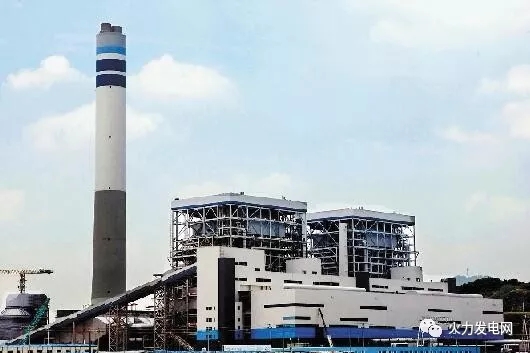
对该机组超低排放改造前后烟气脱硫、脱硝、除尘系统进行了性能试验,结果表明烟囱入口烟尘、SO2、NOx质量浓度分别为4.0、21.5和38.2mg/m3,达到了烟尘、SO2、NOx的排放浓度分别控制在5、35、50mg/m3以内的超低排放要求。改造后,在现有烟气脱硫、脱硝、静电除尘装置的基础上每年可减少烟尘排放量543t、SO2排放量2633t、NOx排放量634t,改善了重点区域空气质量。
煤炭是我国的主要一次能源,煤燃烧过程中产生的SO2、NOx和烟尘是我国大气的主要污染物。近年来我国频繁发生了大面积的严重雾霾天气,给工农业生产和人民的身体健康带来严重的影响,燃煤污染物控制形势日趋严峻。为此,2011年我国颁布了严格的《火电厂大气污染物排放标准》(GB13223—2011),将燃煤火力发电厂烟尘、SO2、NOx等污染物排放浓度限值分别降至30、100、100mg/m3,重点地区降至20、50、100mg/m3。
2014年《煤电节能减排升级与改造行动计划(2014—2020年)》对燃煤烟气中烟尘、SO2、NOx的排放浓度提出了要求新建燃煤机组大气污染物排放基本达到燃气轮机机组排放限值,即在基准氧含量6%的条件下,烟尘、SO2、NOx的排放浓度分别不高于10、35、50mg/m3。
目前国内外对燃煤电厂烟气多种污染物超低排放与协同脱除开展了大量的研究与工程应用,欧美日等发达国家部分电厂已率先实现了燃煤烟气主要污染物排放浓度达到超低排放的要求。
日本碧南电厂1000MW机组采用低NOx燃烧器和空气分级燃烧技术、SCR烟气脱硝、低低温静电除尘器、湿法烟气脱硫和湿式静电除尘器实现了烟尘、SO2、NOx排放浓度分别为3、30和25mg/m3。
2014年5月浙江能源集团嘉兴电厂1000MW机组率先实施超低排放改造并投入运行,测试结果表明主要污染物烟尘、SO2、NOx排放浓度分别达到了2.12、17.47和38.94mg/m3。目前我国各发电集团相继实施了燃煤发电机组的超低排放技术改造,并制定了明确时间表,开启了我国燃煤火力发电机组超低排放改造的新局面。
本文针对国内某1000MW燃烧发电机组主要污染物的排放现状,分析了燃煤机组主要污染物超低排放的技术路线,实施了切实可行的超低排放技术改造工程,进行了超低排放改造前后烟气脱硫、脱硝和除尘性能测试,烟气主要污染物烟尘、SO2、NOx排放浓度分别低于5、35、50mg/m3,有效改善了重点区域空气质量。
1、1000MW燃煤机组污染物排放现状
某电厂2台1000MW机组锅炉为东方锅炉厂制造的超超临界一次中间再热直流锅炉,为超超临界参数变压直流炉、对冲燃烧方式、固态排渣、单炉膛、一次再热、全悬吊п型结构。采用东方锅炉厂引进技术生产的旋流燃烧器前后墙对冲燃烧,燃用晋南、晋东南地区贫煤、烟煤的混合煤种。燃烧系统采用空气分级燃烧和浓淡燃烧等技术,可有效降低NOx排放量和降低锅炉最低稳燃负荷。
烟气脱硫装置为一炉一塔配置的喷淋塔,采用石灰石-石膏湿法烟气脱硫工艺,吸收塔配置4层喷淋层和4台浆液循环泵。在燃用收到基含硫量为1.8%的设计煤种时(对应的脱硫塔入口SO2质量浓度为3900mg/m3)设计脱硫效率不小于95%,脱硫塔出口SO2排放浓度在195mg/m3左右。
选择性催化还原烟气脱硝(SCR)装置催化剂层数按“2+1”模式布置,初装2层预留1层。目前投运2层催化剂,SCR脱硝装置可有效地控制NOx排放浓度在80mg/m3。锅炉尾部配备2台3室4电场的干式静电除尘器,对原有除尘器进行了高频电源改造后,除尘器出口烟尘质量浓度可达到39.8mg/m3。
从以上数据可以看出,虽然该机组依据2011年的排放标准进行了增容提效改造,但现有的烟气脱硫、脱硝、除尘装置不能满足超低排放NOx、SO2、烟尘排放分别低于50、35、5mg/m3。因此,该机组于2016年底实施了超低排放技术改造。
2、1000MW燃煤机组超低排放改造工程
环保岛超低排放技术是对目前燃煤电站的污染物控制技术的整合,在实现超低排放目标的同时有机协调各部分污染物减排装置,以达到NOx、SO2和烟尘等污染物的协同脱除。其中低低温静电除尘器和湿式静电除尘器以其高效的除尘性能及污染物联合脱除性能,逐渐成为多种污染物协同脱除技术的核心。
2.1、烟气脱硫系统改造
该电厂2台1000MW机组脱硫装置自2012年投运以来,净烟气SO2浓度满足小于200mg/m3排放限值环保要求,但无法满足《火电厂大气污染物排放标准》中关于重点地区不超过50mg/m3的SO2排放限值,更无法满足超低排放SO2浓度不超过35mg/m3的要求。
为了满足新的超低排放要求,需要对1000MW燃煤机组脱硫装置进行增容提效改造。根据电厂近年来实际燃用煤种硫含量,结合当前石灰石-石膏湿法单塔脱硫装置提效改造的技术水平及改造后要达到的出口SO2质量浓度不超过35mg/m3的控制目标,本次脱硫提效改造设计煤种收到基含硫量(Sar)按1.5%考虑,即原烟气中SO2浓度按3350mg/m3(标态,干基,6%O2,下同)考虑,要求脱硫系统效率≥99%。
本次改造喷淋吸收塔新增1层喷淋层和1层合金托盘,改造后按5层喷淋层(其中4层投运1层备用)加1层合金托盘设置。原吸收塔入口烟道上沿至底层喷淋层之间距离为3m,利用此空间增设1层不锈钢材质、3mm厚度的合金托盘。
改造原有的4层喷淋层,并在原顶层喷淋层上方新增1层喷淋层,喷淋层间距为2m,新增喷淋层对应设置一台浆液循环泵,改造喷淋层及新增喷淋层对应循环泵流量均为14000m3/h。为保证可靠的脱硫效率,本次改造增加了喷淋层喷嘴数目,提高喷淋层覆盖率,单层喷淋覆盖率不小于300%,并采用单向双头高效喷嘴。为防止吸收塔边壁烟气逃逸,每2层喷淋层之间设置塔壁聚气环。
考虑吸收塔协同除尘效果,拆除原有两级屋脊式除雾器,新增塔内三级高效屋脊式除雾器和一级烟道除雾器,并增加相应的冲洗管路,烟道除雾器冲洗水按返回吸收塔设计。脱硫后的烟气夹带的液滴在吸收塔出口的除雾器中收集,使净烟气的液滴含量不超过15mg/m3。
2.2、SCR烟气脱硝系统改造
烟气脱硝装置采用选择性催化还原烟气脱硝(SCR)技术,催化剂层数按“2+1”模式布置,脱硝还原剂用液氨,SCR脱硝装置设计入口NOx质量浓度为550mg/m3。在设计煤种及校核煤种、锅炉最大连续出力工况(BMCR)、氨逃逸浓度不大于3μL/L情况下,初装的2层催化剂时SCR最大脱硝效率为83.3%。
此次SCR烟气脱硝改造方案为增加1层备用层催化剂并更换1层催化剂,改造后原入口NOx浓度不变,脱硝反应器出口NOx质量浓度要求降低到50mg/m3以内,其脱硝效率≥90.9%。改造后性能试验时脱硝效率不低于92.8%,NOx排放浓度为38.2mg/m3。
综合以上SCR装置性能评估,在现有SCR烟气脱硝基础上按照“2+1”模式增加1层备用层催化剂并更换1层催化剂,进一步提高了SCR脱硝效率,实现了低于50mg/m3的NOx超低排放控制目标。
2.3、烟尘超低排放改造
目前国内外燃煤电厂多采用静电除尘器、电袋复合除尘器等除尘技术,湿式脱硫吸收塔具有协同脱除烟尘的效果。为了进一步大幅度降低燃煤电厂烟尘排放浓度,目前主要采用低低温静电除尘器、湿式静电除尘器或其组合技术。
2.3.1、低低温静电除尘器
低低温省煤器布置在空气预热器与静电除尘器之间,对锅炉排烟进行余热回收利用,烟气温度从通常的130~140℃降到90℃左右,回收的烟气余热用于加热锅炉给水或加热燃烧所需的空气以进一步提高机组的效率和降低供电煤耗。烟气温度对静电除尘器灰比电阻和除尘效率的影响参见文献。
当进入静电除尘器的烟气温度从通常的130~140℃降低至90~100℃时,飞灰比电阻降低了1个数量级以上,而且对于不同的煤种其飞灰比电阻降低幅度有所不同。飞灰比电阻的降低可以避免反电晕现象,大幅度提高静电除尘器除尘效率。但飞灰比电阻的降低会加剧二次扬尘现象的产生,这需要采取针对性措施,才能保证烟尘排放浓度低于常规静电除尘器。
寿春晖等[8]研究了某百万千瓦机组进行颗粒物脱除特性,结果表明采用低低温静电除尘器后,对粒径>10μm的烟尘的脱除效率高达99%。与此同时,烟气温度降低促进了烟气中SO3与水蒸气结合生成硫酸雾,易被飞灰颗粒吸附,吸附了SO3的烟尘颗粒进入静电除尘器后,被静电除尘器捕集排出,不仅解决了下游设备的防腐蚀难题,还提高了后续脱硫吸收塔的脱硫效率,降低了脱硫耗水量。
烟气温度降低减小了烟气体积,降低引风机的电耗,但加装低低温省煤器会增加烟气阻力损失。另外,除尘后的低温烟气能达到湿法脱硫工艺的烟温要求,不必再加装GGH换热器来降低烟温。
2.3.2、湿法烟气脱硫协同除尘
近年来,众多学者在研究湿法烟气脱硫吸收塔高效脱硫的基础上,研究了其除尘性能的协同作用。脱硫吸收塔除尘主要包括了脱硫吸收区除尘和除雾器区除尘。烟气进入脱硫吸收塔后,烟尘与雾化后的液滴之间相互碰撞,经集聚和沉降作用被石灰石浆液液滴捕捉。
被液滴捕捉的一部分烟尘在重力作用下从吸收区落入到浆液池中,达到了捕捉烟尘的效果。另一部分细小液滴在除雾器的弯曲通道内凝聚,当自身重力大于烟气升力和液体表面张力时,烟尘从除雾器上落入到浆液池中,实现液滴回收和脱除烟尘的目的。
王翱等、王珲等对脱硫吸收塔内细颗粒物的捕集性能进行了试验研究和数值模拟,结果表明湿式脱硫吸收塔对于2.5μm以上的颗粒物具有较高的脱除性能,可达到74.5%的脱除效率。因此,湿法脱硫吸收塔协同除尘可进一步降低烟尘排放浓度。
2.3.3、湿式静电除尘器
近30年来,湿式静电除尘器(WESP)在欧美和日本等发达国家已取得较好的成效。日本三菱重工在碧南电厂采用WESP技术投产近20年来,烟尘排放浓度控制在2~5mg/m3。WESP在国内电厂应用处于起步阶段,随着国家对烟尘排放指标要求越来越严格,WESP将成为控制细小颗粒物的重要手段。
湿式静电除尘器的工作原理为在干式静电除尘器的基础上安装连续水膜和喷淋装置,烟气中粉尘在电极作用下,电子和正离子附着在粉尘表面,促使粉尘在集尘极表面富集,被连续水膜冲走,达到高效除尘的效果,尤其对PM2.5和硫酸烟雾具有较高脱除作用。湿式静电除尘器的使用,不仅可以满足烟尘超低排放的要求,同时能够减轻石膏雨和蓝色烟雾等污染。
熊桂龙等研究了WESP的脱除机理和对细小颗粒物的分级脱除效率,结果表明WESP对亚微米级的细小颗粒具有较高的脱除效率。赵磊等对几种不同极板的湿式静电除尘器性能进行比较,认为线板式湿式静电除尘器对大于10μm和小于1μm的烟尘有更好的除尘效果。
采用DPI细颗粒物采样仪对某300MW燃煤机组采用湿式静电除尘器前后进行采样测试,烟气中颗粒物浓度由16.1mg/m3降低至1.8mg/m3,脱除效率达88%。
Sui等采用ELPI+取样分析系统测量了三河电厂300MW超低排放机组低低温静电除尘器、烟气脱硫吸收塔以及湿式静电除尘器进出口的细颗粒物排放浓度和粒径分布,结果表明采用低低温静电除尘器、提高湿法烟气脱硫的洗涤效果和改进除雾器性能等措施后烟尘浓度可达到超低排放标准,进一步采用湿式静电除尘器烟气中细颗粒物排放浓度低于1mg/m3。
2.4、超低排放改造工程实施方案
基于此次超低排放改造工程目标要求,结合机组实际运行条件和脱硫装置结构,该机组超低排放改造采用“SCR脱硝增容+低低温静电除尘器+高频静电除尘器改造+脱硫吸收塔提效与协同除尘”的技术方案,如图1所示。采用低低温省煤器回收利用烟气余热加热锅炉给水,提高机组效率和降低供电煤耗。
用低低温省煤器将锅炉排烟温度从139℃降低到94℃左右,提高了低低温静电除尘器除尘效率。在原静电除尘器前加装一个高频电源的电场,并对原电场进行高频电源改造,静电除尘器原第4电场的高频电源移至第3电场,第1、4电场的电源采用进口高频电源。同时完善了低低温静电除尘器配套设施,在静电除尘器绝缘子位置加装了强制热
风吹扫装置,电场所有灰斗采用蒸汽加热改造。检查更换1,2,3电场内部损坏的极板,更换内部损坏的极线、极板,电场内部气流分布装置、漏风、振打等检查、修复与调整,改造各电场输灰系统。
在现有SCR烟气脱硝基础上按照“2+1”模式增加1层备用层催化剂并更换1层催化剂,进一步提高SCR脱硝效率,实现了低于50mg/m3的NOx超低排放控制目标。本次改造喷淋吸收塔新增1层喷淋层及1层合金托盘,即改造后脱硫吸收塔设置了1层喷淋层(其中4层投运、1层备用)和1层合金托盘。
脱硫改造中增装了1层合金托盘,大部分细小烟尘经过托盘的筛孔进入泡沫层,受泡沫扰动的影响而改变方向,从而增加了与液体接触的机理,达到除尘净化效果。同时将塔内原两级除雾器拆除,新增了三级高效屋脊式除雾器和一级烟道除雾器,能够有效提高脱硫塔对烟尘的脱除效果。
通过采用静电除尘器高频电源改造、低低温静电除尘器以及湿式脱硫吸收塔协同除尘和高效多级除雾器等组合措施,脱硫塔出口烟尘浓度可降低到5mg/m3以下,并预留了湿式静电除尘器的安装空间。当燃用高灰量的煤种以及烟尘排放浓度限值更加严格时,可在脱硫吸收塔后安装湿式静电除尘器。
3燃煤机组超低排放改造工程效果
3.1超低排放改造工程性能试验结果
通过对该电厂1000MW机组烟气脱硫、脱硝、除尘装置进行了性能考核试验,主要测试结论如下:1)机组负荷986.6MW,实测脱硫装置出口烟气流量为342.1×104m3/h,脱硫装置入口烟气温度为98.4℃,脱硫装置出口烟气温度为49.0℃。
2)脱硫装置入口原烟气SO2质量浓度2301.1mg/m3,脱硫装置出口净烟气SO2质量浓度21.5mg/m3,SO2脱除效率99.04%。脱硫装置出口净烟气SO2质量浓度≤35mg/m3,脱硫装置SO2脱除效率及净烟气SO2排放浓度均满足设计值要求。
3)SCR反应器入口NOx平均质量浓度为549.4mg/m3,反应器出口NOx平均质量浓度为38.2mg/m3,低于50mg/m3的设计值,脱硝效率为93.1%。
4)测得各个不同位置烟尘浓度如图2所示,低低温静电除尘器入口烟尘质量浓度24.33g/m3,脱硫吸收塔入口烟尘质量浓度23.0mg/m3,低低温静电除尘器除尘效率99.91%。脱硫吸收塔出口净烟气粉尘质量浓度的实测平均值为4.8mg/m3,烟囱入口净烟气粉尘质量浓度的实测平均值为4.0mg/m3。
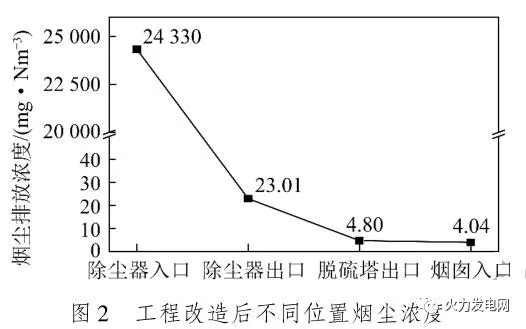
吸收塔出口、烟囱入口粉尘质量浓度均≤5mg/m3,满足设计要求。该1000MW超低排放改造后,烟囱入口烟尘、SO2、NOx质量浓度分别为4.0、21.5和38.2mg/m3,均达到燃煤机组/各污染物超低排放的要求。
3.2、超低排放改造经济社会与环保效益分析
采用上述“SCR脱硝增容+低低温静电除尘器+高频静电除尘器改造+脱硫吸收塔提效与协同除尘”的超低排放技术方案对某1000MW燃煤机组进行技术改造后,烟囱入口烟尘、SO2、NOx质量浓度分别为4.0、21.5和38.2mg/m3,达到了排烟中烟尘、SO2、NOx的排放浓度分别控制在5、35、50mg/m3以内的超低排放要求。
与超低排放改造前该燃煤机组各污染物排放浓度相比,改造后烟尘、SO2、NOx排放浓度分别降低了35.8、173.5和58.5mg/m3。
按该机组烟气量为3372811m3/h和年运行4500h计算,在现有烟气脱硫、脱硝、除尘装置基础上每年可进一步减少烟尘排放量543t、SO2排放量2633t、NOx排放量634t,满足燃煤机组大气污染物超低排放限值的要求,并明显改善当地空气质量。
4结论
1)根据国家节能减排的要求,低低温静电除尘器和湿式静电除尘器凭借其高效的除尘性能和广泛的适用性逐渐成为燃煤火电机组实现超低排放的有效途径。
2)采用“SCR脱硝增容+低低温静电除尘器+高频静电除尘器改造+脱硫吸收塔提效与协同除尘”的超低排放技术方案对某1000MW燃煤机组进行技术改造后,烟囱入口烟尘、SO2、NOx质量浓度分别为4.0、21.5和38.2mg/m3,达到了排烟中烟尘、SO2、NOx的排放浓度分别控制在5、35、50mg/m3以内的超低排放要求。
3)实施上述超低排放改造后,1000MW燃煤机组在现有烟气脱硫、脱硝、除尘装置的基础上每年可进一步减少烟尘排放量543t、SO2排放量2633t、NOx排放量634t,改善了重点区域空气质量。
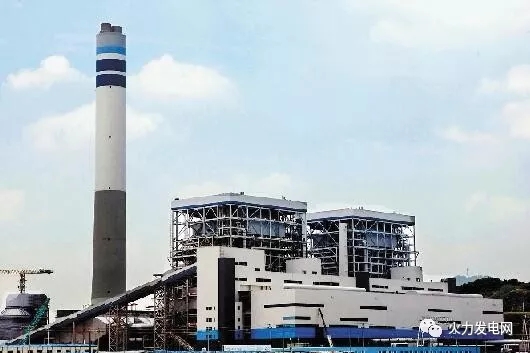
对该机组超低排放改造前后烟气脱硫、脱硝、除尘系统进行了性能试验,结果表明烟囱入口烟尘、SO2、NOx质量浓度分别为4.0、21.5和38.2mg/m3,达到了烟尘、SO2、NOx的排放浓度分别控制在5、35、50mg/m3以内的超低排放要求。改造后,在现有烟气脱硫、脱硝、静电除尘装置的基础上每年可减少烟尘排放量543t、SO2排放量2633t、NOx排放量634t,改善了重点区域空气质量。
煤炭是我国的主要一次能源,煤燃烧过程中产生的SO2、NOx和烟尘是我国大气的主要污染物。近年来我国频繁发生了大面积的严重雾霾天气,给工农业生产和人民的身体健康带来严重的影响,燃煤污染物控制形势日趋严峻。为此,2011年我国颁布了严格的《火电厂大气污染物排放标准》(GB13223—2011),将燃煤火力发电厂烟尘、SO2、NOx等污染物排放浓度限值分别降至30、100、100mg/m3,重点地区降至20、50、100mg/m3。
2014年《煤电节能减排升级与改造行动计划(2014—2020年)》对燃煤烟气中烟尘、SO2、NOx的排放浓度提出了要求新建燃煤机组大气污染物排放基本达到燃气轮机机组排放限值,即在基准氧含量6%的条件下,烟尘、SO2、NOx的排放浓度分别不高于10、35、50mg/m3。
目前国内外对燃煤电厂烟气多种污染物超低排放与协同脱除开展了大量的研究与工程应用,欧美日等发达国家部分电厂已率先实现了燃煤烟气主要污染物排放浓度达到超低排放的要求。
日本碧南电厂1000MW机组采用低NOx燃烧器和空气分级燃烧技术、SCR烟气脱硝、低低温静电除尘器、湿法烟气脱硫和湿式静电除尘器实现了烟尘、SO2、NOx排放浓度分别为3、30和25mg/m3。
2014年5月浙江能源集团嘉兴电厂1000MW机组率先实施超低排放改造并投入运行,测试结果表明主要污染物烟尘、SO2、NOx排放浓度分别达到了2.12、17.47和38.94mg/m3。目前我国各发电集团相继实施了燃煤发电机组的超低排放技术改造,并制定了明确时间表,开启了我国燃煤火力发电机组超低排放改造的新局面。
本文针对国内某1000MW燃烧发电机组主要污染物的排放现状,分析了燃煤机组主要污染物超低排放的技术路线,实施了切实可行的超低排放技术改造工程,进行了超低排放改造前后烟气脱硫、脱硝和除尘性能测试,烟气主要污染物烟尘、SO2、NOx排放浓度分别低于5、35、50mg/m3,有效改善了重点区域空气质量。
1、1000MW燃煤机组污染物排放现状
某电厂2台1000MW机组锅炉为东方锅炉厂制造的超超临界一次中间再热直流锅炉,为超超临界参数变压直流炉、对冲燃烧方式、固态排渣、单炉膛、一次再热、全悬吊п型结构。采用东方锅炉厂引进技术生产的旋流燃烧器前后墙对冲燃烧,燃用晋南、晋东南地区贫煤、烟煤的混合煤种。燃烧系统采用空气分级燃烧和浓淡燃烧等技术,可有效降低NOx排放量和降低锅炉最低稳燃负荷。
烟气脱硫装置为一炉一塔配置的喷淋塔,采用石灰石-石膏湿法烟气脱硫工艺,吸收塔配置4层喷淋层和4台浆液循环泵。在燃用收到基含硫量为1.8%的设计煤种时(对应的脱硫塔入口SO2质量浓度为3900mg/m3)设计脱硫效率不小于95%,脱硫塔出口SO2排放浓度在195mg/m3左右。
选择性催化还原烟气脱硝(SCR)装置催化剂层数按“2+1”模式布置,初装2层预留1层。目前投运2层催化剂,SCR脱硝装置可有效地控制NOx排放浓度在80mg/m3。锅炉尾部配备2台3室4电场的干式静电除尘器,对原有除尘器进行了高频电源改造后,除尘器出口烟尘质量浓度可达到39.8mg/m3。
从以上数据可以看出,虽然该机组依据2011年的排放标准进行了增容提效改造,但现有的烟气脱硫、脱硝、除尘装置不能满足超低排放NOx、SO2、烟尘排放分别低于50、35、5mg/m3。因此,该机组于2016年底实施了超低排放技术改造。
2、1000MW燃煤机组超低排放改造工程
环保岛超低排放技术是对目前燃煤电站的污染物控制技术的整合,在实现超低排放目标的同时有机协调各部分污染物减排装置,以达到NOx、SO2和烟尘等污染物的协同脱除。其中低低温静电除尘器和湿式静电除尘器以其高效的除尘性能及污染物联合脱除性能,逐渐成为多种污染物协同脱除技术的核心。
2.1、烟气脱硫系统改造
该电厂2台1000MW机组脱硫装置自2012年投运以来,净烟气SO2浓度满足小于200mg/m3排放限值环保要求,但无法满足《火电厂大气污染物排放标准》中关于重点地区不超过50mg/m3的SO2排放限值,更无法满足超低排放SO2浓度不超过35mg/m3的要求。
为了满足新的超低排放要求,需要对1000MW燃煤机组脱硫装置进行增容提效改造。根据电厂近年来实际燃用煤种硫含量,结合当前石灰石-石膏湿法单塔脱硫装置提效改造的技术水平及改造后要达到的出口SO2质量浓度不超过35mg/m3的控制目标,本次脱硫提效改造设计煤种收到基含硫量(Sar)按1.5%考虑,即原烟气中SO2浓度按3350mg/m3(标态,干基,6%O2,下同)考虑,要求脱硫系统效率≥99%。
本次改造喷淋吸收塔新增1层喷淋层和1层合金托盘,改造后按5层喷淋层(其中4层投运1层备用)加1层合金托盘设置。原吸收塔入口烟道上沿至底层喷淋层之间距离为3m,利用此空间增设1层不锈钢材质、3mm厚度的合金托盘。
改造原有的4层喷淋层,并在原顶层喷淋层上方新增1层喷淋层,喷淋层间距为2m,新增喷淋层对应设置一台浆液循环泵,改造喷淋层及新增喷淋层对应循环泵流量均为14000m3/h。为保证可靠的脱硫效率,本次改造增加了喷淋层喷嘴数目,提高喷淋层覆盖率,单层喷淋覆盖率不小于300%,并采用单向双头高效喷嘴。为防止吸收塔边壁烟气逃逸,每2层喷淋层之间设置塔壁聚气环。
考虑吸收塔协同除尘效果,拆除原有两级屋脊式除雾器,新增塔内三级高效屋脊式除雾器和一级烟道除雾器,并增加相应的冲洗管路,烟道除雾器冲洗水按返回吸收塔设计。脱硫后的烟气夹带的液滴在吸收塔出口的除雾器中收集,使净烟气的液滴含量不超过15mg/m3。
2.2、SCR烟气脱硝系统改造
烟气脱硝装置采用选择性催化还原烟气脱硝(SCR)技术,催化剂层数按“2+1”模式布置,脱硝还原剂用液氨,SCR脱硝装置设计入口NOx质量浓度为550mg/m3。在设计煤种及校核煤种、锅炉最大连续出力工况(BMCR)、氨逃逸浓度不大于3μL/L情况下,初装的2层催化剂时SCR最大脱硝效率为83.3%。
此次SCR烟气脱硝改造方案为增加1层备用层催化剂并更换1层催化剂,改造后原入口NOx浓度不变,脱硝反应器出口NOx质量浓度要求降低到50mg/m3以内,其脱硝效率≥90.9%。改造后性能试验时脱硝效率不低于92.8%,NOx排放浓度为38.2mg/m3。
综合以上SCR装置性能评估,在现有SCR烟气脱硝基础上按照“2+1”模式增加1层备用层催化剂并更换1层催化剂,进一步提高了SCR脱硝效率,实现了低于50mg/m3的NOx超低排放控制目标。
2.3、烟尘超低排放改造
目前国内外燃煤电厂多采用静电除尘器、电袋复合除尘器等除尘技术,湿式脱硫吸收塔具有协同脱除烟尘的效果。为了进一步大幅度降低燃煤电厂烟尘排放浓度,目前主要采用低低温静电除尘器、湿式静电除尘器或其组合技术。
2.3.1、低低温静电除尘器
低低温省煤器布置在空气预热器与静电除尘器之间,对锅炉排烟进行余热回收利用,烟气温度从通常的130~140℃降到90℃左右,回收的烟气余热用于加热锅炉给水或加热燃烧所需的空气以进一步提高机组的效率和降低供电煤耗。烟气温度对静电除尘器灰比电阻和除尘效率的影响参见文献。
当进入静电除尘器的烟气温度从通常的130~140℃降低至90~100℃时,飞灰比电阻降低了1个数量级以上,而且对于不同的煤种其飞灰比电阻降低幅度有所不同。飞灰比电阻的降低可以避免反电晕现象,大幅度提高静电除尘器除尘效率。但飞灰比电阻的降低会加剧二次扬尘现象的产生,这需要采取针对性措施,才能保证烟尘排放浓度低于常规静电除尘器。
寿春晖等[8]研究了某百万千瓦机组进行颗粒物脱除特性,结果表明采用低低温静电除尘器后,对粒径>10μm的烟尘的脱除效率高达99%。与此同时,烟气温度降低促进了烟气中SO3与水蒸气结合生成硫酸雾,易被飞灰颗粒吸附,吸附了SO3的烟尘颗粒进入静电除尘器后,被静电除尘器捕集排出,不仅解决了下游设备的防腐蚀难题,还提高了后续脱硫吸收塔的脱硫效率,降低了脱硫耗水量。
烟气温度降低减小了烟气体积,降低引风机的电耗,但加装低低温省煤器会增加烟气阻力损失。另外,除尘后的低温烟气能达到湿法脱硫工艺的烟温要求,不必再加装GGH换热器来降低烟温。
2.3.2、湿法烟气脱硫协同除尘
近年来,众多学者在研究湿法烟气脱硫吸收塔高效脱硫的基础上,研究了其除尘性能的协同作用。脱硫吸收塔除尘主要包括了脱硫吸收区除尘和除雾器区除尘。烟气进入脱硫吸收塔后,烟尘与雾化后的液滴之间相互碰撞,经集聚和沉降作用被石灰石浆液液滴捕捉。
被液滴捕捉的一部分烟尘在重力作用下从吸收区落入到浆液池中,达到了捕捉烟尘的效果。另一部分细小液滴在除雾器的弯曲通道内凝聚,当自身重力大于烟气升力和液体表面张力时,烟尘从除雾器上落入到浆液池中,实现液滴回收和脱除烟尘的目的。
王翱等、王珲等对脱硫吸收塔内细颗粒物的捕集性能进行了试验研究和数值模拟,结果表明湿式脱硫吸收塔对于2.5μm以上的颗粒物具有较高的脱除性能,可达到74.5%的脱除效率。因此,湿法脱硫吸收塔协同除尘可进一步降低烟尘排放浓度。
2.3.3、湿式静电除尘器
近30年来,湿式静电除尘器(WESP)在欧美和日本等发达国家已取得较好的成效。日本三菱重工在碧南电厂采用WESP技术投产近20年来,烟尘排放浓度控制在2~5mg/m3。WESP在国内电厂应用处于起步阶段,随着国家对烟尘排放指标要求越来越严格,WESP将成为控制细小颗粒物的重要手段。
湿式静电除尘器的工作原理为在干式静电除尘器的基础上安装连续水膜和喷淋装置,烟气中粉尘在电极作用下,电子和正离子附着在粉尘表面,促使粉尘在集尘极表面富集,被连续水膜冲走,达到高效除尘的效果,尤其对PM2.5和硫酸烟雾具有较高脱除作用。湿式静电除尘器的使用,不仅可以满足烟尘超低排放的要求,同时能够减轻石膏雨和蓝色烟雾等污染。
熊桂龙等研究了WESP的脱除机理和对细小颗粒物的分级脱除效率,结果表明WESP对亚微米级的细小颗粒具有较高的脱除效率。赵磊等对几种不同极板的湿式静电除尘器性能进行比较,认为线板式湿式静电除尘器对大于10μm和小于1μm的烟尘有更好的除尘效果。
采用DPI细颗粒物采样仪对某300MW燃煤机组采用湿式静电除尘器前后进行采样测试,烟气中颗粒物浓度由16.1mg/m3降低至1.8mg/m3,脱除效率达88%。
Sui等采用ELPI+取样分析系统测量了三河电厂300MW超低排放机组低低温静电除尘器、烟气脱硫吸收塔以及湿式静电除尘器进出口的细颗粒物排放浓度和粒径分布,结果表明采用低低温静电除尘器、提高湿法烟气脱硫的洗涤效果和改进除雾器性能等措施后烟尘浓度可达到超低排放标准,进一步采用湿式静电除尘器烟气中细颗粒物排放浓度低于1mg/m3。
2.4、超低排放改造工程实施方案
基于此次超低排放改造工程目标要求,结合机组实际运行条件和脱硫装置结构,该机组超低排放改造采用“SCR脱硝增容+低低温静电除尘器+高频静电除尘器改造+脱硫吸收塔提效与协同除尘”的技术方案,如图1所示。采用低低温省煤器回收利用烟气余热加热锅炉给水,提高机组效率和降低供电煤耗。
用低低温省煤器将锅炉排烟温度从139℃降低到94℃左右,提高了低低温静电除尘器除尘效率。在原静电除尘器前加装一个高频电源的电场,并对原电场进行高频电源改造,静电除尘器原第4电场的高频电源移至第3电场,第1、4电场的电源采用进口高频电源。同时完善了低低温静电除尘器配套设施,在静电除尘器绝缘子位置加装了强制热
风吹扫装置,电场所有灰斗采用蒸汽加热改造。检查更换1,2,3电场内部损坏的极板,更换内部损坏的极线、极板,电场内部气流分布装置、漏风、振打等检查、修复与调整,改造各电场输灰系统。
在现有SCR烟气脱硝基础上按照“2+1”模式增加1层备用层催化剂并更换1层催化剂,进一步提高SCR脱硝效率,实现了低于50mg/m3的NOx超低排放控制目标。本次改造喷淋吸收塔新增1层喷淋层及1层合金托盘,即改造后脱硫吸收塔设置了1层喷淋层(其中4层投运、1层备用)和1层合金托盘。
脱硫改造中增装了1层合金托盘,大部分细小烟尘经过托盘的筛孔进入泡沫层,受泡沫扰动的影响而改变方向,从而增加了与液体接触的机理,达到除尘净化效果。同时将塔内原两级除雾器拆除,新增了三级高效屋脊式除雾器和一级烟道除雾器,能够有效提高脱硫塔对烟尘的脱除效果。
通过采用静电除尘器高频电源改造、低低温静电除尘器以及湿式脱硫吸收塔协同除尘和高效多级除雾器等组合措施,脱硫塔出口烟尘浓度可降低到5mg/m3以下,并预留了湿式静电除尘器的安装空间。当燃用高灰量的煤种以及烟尘排放浓度限值更加严格时,可在脱硫吸收塔后安装湿式静电除尘器。
3燃煤机组超低排放改造工程效果
3.1超低排放改造工程性能试验结果
通过对该电厂1000MW机组烟气脱硫、脱硝、除尘装置进行了性能考核试验,主要测试结论如下:1)机组负荷986.6MW,实测脱硫装置出口烟气流量为342.1×104m3/h,脱硫装置入口烟气温度为98.4℃,脱硫装置出口烟气温度为49.0℃。
2)脱硫装置入口原烟气SO2质量浓度2301.1mg/m3,脱硫装置出口净烟气SO2质量浓度21.5mg/m3,SO2脱除效率99.04%。脱硫装置出口净烟气SO2质量浓度≤35mg/m3,脱硫装置SO2脱除效率及净烟气SO2排放浓度均满足设计值要求。
3)SCR反应器入口NOx平均质量浓度为549.4mg/m3,反应器出口NOx平均质量浓度为38.2mg/m3,低于50mg/m3的设计值,脱硝效率为93.1%。
4)测得各个不同位置烟尘浓度如图2所示,低低温静电除尘器入口烟尘质量浓度24.33g/m3,脱硫吸收塔入口烟尘质量浓度23.0mg/m3,低低温静电除尘器除尘效率99.91%。脱硫吸收塔出口净烟气粉尘质量浓度的实测平均值为4.8mg/m3,烟囱入口净烟气粉尘质量浓度的实测平均值为4.0mg/m3。
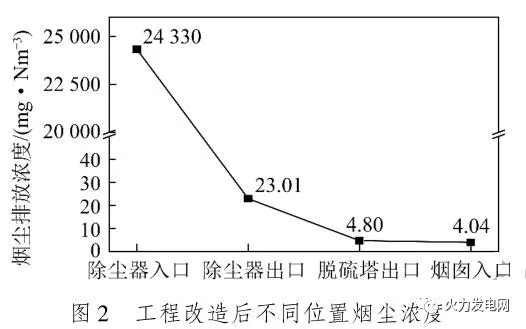
吸收塔出口、烟囱入口粉尘质量浓度均≤5mg/m3,满足设计要求。该1000MW超低排放改造后,烟囱入口烟尘、SO2、NOx质量浓度分别为4.0、21.5和38.2mg/m3,均达到燃煤机组/各污染物超低排放的要求。
3.2、超低排放改造经济社会与环保效益分析
采用上述“SCR脱硝增容+低低温静电除尘器+高频静电除尘器改造+脱硫吸收塔提效与协同除尘”的超低排放技术方案对某1000MW燃煤机组进行技术改造后,烟囱入口烟尘、SO2、NOx质量浓度分别为4.0、21.5和38.2mg/m3,达到了排烟中烟尘、SO2、NOx的排放浓度分别控制在5、35、50mg/m3以内的超低排放要求。
与超低排放改造前该燃煤机组各污染物排放浓度相比,改造后烟尘、SO2、NOx排放浓度分别降低了35.8、173.5和58.5mg/m3。
按该机组烟气量为3372811m3/h和年运行4500h计算,在现有烟气脱硫、脱硝、除尘装置基础上每年可进一步减少烟尘排放量543t、SO2排放量2633t、NOx排放量634t,满足燃煤机组大气污染物超低排放限值的要求,并明显改善当地空气质量。
4结论
1)根据国家节能减排的要求,低低温静电除尘器和湿式静电除尘器凭借其高效的除尘性能和广泛的适用性逐渐成为燃煤火电机组实现超低排放的有效途径。
2)采用“SCR脱硝增容+低低温静电除尘器+高频静电除尘器改造+脱硫吸收塔提效与协同除尘”的超低排放技术方案对某1000MW燃煤机组进行技术改造后,烟囱入口烟尘、SO2、NOx质量浓度分别为4.0、21.5和38.2mg/m3,达到了排烟中烟尘、SO2、NOx的排放浓度分别控制在5、35、50mg/m3以内的超低排放要求。
3)实施上述超低排放改造后,1000MW燃煤机组在现有烟气脱硫、脱硝、除尘装置的基础上每年可进一步减少烟尘排放量543t、SO2排放量2633t、NOx排放量634t,改善了重点区域空气质量。
