摘 要:计算机技术的发展给传统制造加工业带来了根本性改革,从而进入了现代制造技术时代。当前,数控技术成为制造加工业的关键技术,世界上许多国家投入巨资对现代制造加工技术进行研发,以改革传统的制造加工模式。现代制造系统采用了高精度、高效率、高响应、高智能、高自动化等特征的数控技术。数控技术集成微电子、计算机、信息网络化、 自动加工检测、自动控制等高新技术,对制造业实现柔性自动化、集成化、智能化起着举足轻重的作用。
关键词:智能化机床 数控技术 传统加工
1 数控系统发展趋势
自1952年美国麻省理工学院研制出第一台实验性数控铣床系统出现,到现在已走过了几十年的发展历程。数控系统到目前为止共发展了6代:第一代是电子管数控系统,第二代是晶体管数控系统,第三代是集成电路数控系统,第四代是小型计算机数控系统,第五代是微型计算机数控系统,第六代是 PC 数控系统。原来传统数控系统采用单片机作为处理器,这样带来处理速度慢、存储容量小,然后随着现代加工对加工制造业发展需求越来越大。因此,这种模式越来越不能适应现代加工需要,比如程序存放空间问题,数控程序越来越大,而传统数控系统存放空间不够大。这样情况下就诞生了DNC通讯,但是殊不知这样的模式不能从根本上解决这类问题,而随着计算机发展,程序容量越来越方便、便宜,在这种情况下PC式数控系统开始采用大存储容量的存储设备,从根本上解决这种问题。PC式数控系统目前是先进的结构体系,具备了计算机的一些特性,比如高分辨率的显示、强大的处理速度、灵活方便的操作系统,最大的特性是网络化的普及发展,极大的改变了传统加工的模式。
计算机的发展,随着处理器的功能越来越大,逐渐取代原来NC +PLC这种模式,取而代之的是NC和PLC共用一个处理器,大大降低成本,还能保证处理时序的问题。PLC采用更为灵活的ST语言来编写,减少了程序数量和步骤,也更灵活的实现了逻辑处理能力,而且计算机的扫描周期要远远小于原理的周期,真正实现毫秒级。
2 数控系统的智能化具有以下特性
2.1 操作智能化
智能化的数控系统应该具有底层操作系统,并且通过总线和相关设备通讯,具有高响应,高运算、高速度等特性;同时,系统还具有良好的开放性和人机界面,系统针对不同型号和类型的机床特点,通过KV编辑软件,可以实现对操作界面进行深入定制;另外,系统硬件采用电阻触摸屏,目的是让用户能够实现“一键直达”,最大程度地简化了用户的操作,降低用户的学习和使用成本。
智能化的数控系统,还提供一种全新的图形引导编程方式,引导用户一步一步完成加工步骤,通过图形或动画的方式,用户只需要填写加工所必须的加工参数即可,无需记忆繁琐的步骤,把记忆的工作从人脑中解放出来,最大程度的降低劳动强度。
2.2 加工智能化
智能化的数控系统应该集成三维图形模拟软件,能够对加工过程进行在线和离线实时仿真。有多种工件形状可供选择,如棒料、管型件、六角型件,工件尺寸完全参数化。有多种工装夹具可供选择,加工坐标系自由设定。可以自由选择常见的刀具类型,刀具形状尺寸参数化,主动进行刀具和工件之间的干涉检查。支持各种基本加工工艺的模拟,可以设置工件剖视图,工件内部剖视120度,能够非常直观地看内空的切削效果,避免了实际加工中看不到内部的缺陷,真正实现了材料去除过程一目了然。除标准工艺循环外,智能化的数控系统还应该有高度开放性,来满足不同客户的需求,降低用户编程时间和减少用户输入程序错误的概率,如多个切槽或者加工多头螺纹等。
现在用户编程过程中,对加工参数的选择最为困难,因为所有加工参数都是不断通过实验得出,而这套参数只有该实验人员或相关人员知道,影响了工艺参数的传递。因此,智能化的数控系统需要对工艺这一块的插件,如客户对工艺参数的选择有疑问,可以按键盘上的快捷键,打开工艺参数支持系统界面,里面保存了前面很多位工程师的经验参数,通过设定刀具类型、刀具材料、工件材料、工件形状及加工方式等参数,由系统自动生成主轴转速、进给速度、进给量等工艺参数的推荐值。
每台机床因为机械特性、装配工艺等各有差异,即便是同样的数控系统,应用于不同的机床时,也需要设定不同的参数,以提高机床相应速度、精度等。快速匹配最佳伺服和电机参数,优化机床动态性能,提高加工效率和精度。
2.3 编程智能化
智能化的数控系统,应该具备智能化的编程方式,既能兼容传统的G代码和M代码,保证原来加工程序可以使用,又能提供更灵活的生成程序的途径,如通过三维图形,设置相对应的加工参数,如加工刀具、加工参数等,然后通过引导用户一步一步操作,并最终生成用于加工这一特征的一段(若干行)NC程序。这个全新的功能,可以简化编程步骤,提高编程效率,减少用户输入程序的时间,是智能化数控系统一个亮点。
2.4 维护智能化
首先,智能化的数控系统应具有自身诊断的功能,通过电气检测元器件反馈信号,实时反馈给数控系统机床的故障,并且通过图形化诊断工具用于监控机床各辅助电气部件的工作状态,并且为用户诊断机床电气故障提供帮助,它将每一部件的输入输出点的状态、电气或机械原理通过图形方式展现出来,便于用户直观地监控其工作状态,诊断相应的电气故障。这样电气故障很直观的反馈给用户,方便用户快速诊断故障,并提供解决问题的思路和办法,引导用户一步一步操作,直到最终解决问题。其次,智能化的数控系统还应具备网络诊断功能。如果机床出现任何故障,第一时间将机床的故障发送到维护或管理人员的手机或电子邮箱上,使其第一时间了解到当前机床状态,及时处理机床所发生的故障。有了这种功能,维护人员就不需要24小时停留在生产车间,还应在网盘上自动备份机床相关的操作信息。如果用户的数控机床通过互联网与系统制造商的网络相连接,当机床发生故障时,用户可以通过网络向相关专家请求,相关专家即可通过远程网络服务的方式直接访问该用户数控机床,了解相关的信息,随时可帮助用户快速解决数控系统软件的问题。
2.5 车间智能化
基于DNC技术,利用丰富的高速网络功能,将多台智能化数控系统连接起来,通过PC电脑可观察机床的运转状态和程序状态,又可实时监控加工现场的作业。另外,通过数控机床与工厂的网络相连接,可以使管理部门实时了解机床加工情况,并结合公司的ERP管理软件,及时提醒用户补充相关原材料和消耗品,从而保证车间加工和库存产品两者最大利益化,并统计出每加工一件产品的成本,提供给公司的管理层,帮助公司及时做出合理的决策,实现车间级的智能化和信息化管理(见图1)。
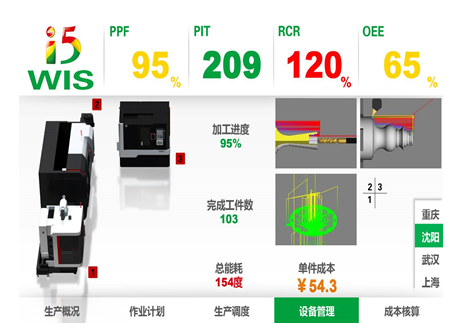
图1 车间的自动化及智能化
3 结语
随着计算机技术和数控系统的不断发展,数控系统的单机智能化和网络智能化已成为数控机床研究的重要领域。由于人工成本越来越贵,机器手等辅助设备的出现陆续替代了人工,这时就对数控设备的兼容性和协调性提出了更高的要求。智能化的数控机床将变得越来越“聪明”和人性化,在将来的工厂里,数控机床不仅是一台加工设备,而是工厂管理网络中的一个节点,具备更加广泛的人机交互、物-物通信功能,从而开创智能数控技术的新篇章。
